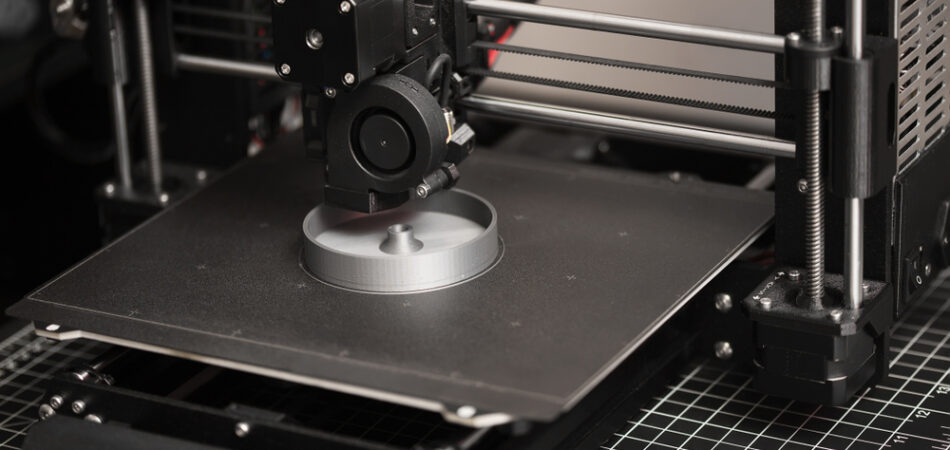
Metal fabrication is a critical industry that supports numerous sectors, from aerospace to automotive. Achieving precision in this field is essential, and recent advancements in technology have made this more attainable than ever. One of the most significant innovations in metal fabrication is the use of 3D modeling tools. This article explores how 3D modeling in metal fabrication enhances precision and contributes to overall efficiency in the industry.
The Importance of Precision in Metal Fabrication
Precision in metal fabrication refers to the ability to create parts and structures that meet exact specifications and tolerances. This is crucial because even minor deviations can lead to significant issues, including reduced performance, safety hazards, and increased costs. Achieving high levels of precision ensures that metal components fit together correctly and function as intended.
The Evolution of Metal Fabrication
Traditionally, metal fabrication relied heavily on manual techniques and trial-and-error methods. As technology has advanced, so too have the tools and methods used in the industry. Early innovations, such as computer numerical control (CNC) machines, revolutionized metal fabrication by introducing automation and increasing accuracy.However, the real game-changer in recent years has been the integration of 3D modeling tools. These digital technologies allow fabricators to design and visualize metal components in a virtual environment before they are physically produced. This not only enhances precision but also streamlines the entire fabrication process.
What is 3D Modeling in Metal Fabrication?
3D modeling in metal fabrication involves creating three-dimensional representations of metal parts or assemblies using specialized software. These digital models provide a detailed view of the final product, including its dimensions, shapes, and intricate features. The 3D model serves as a blueprint that guides the fabrication process, ensuring that each component is manufactured with exact specifications.
Key Advantages of 3D Modeling Tools
- Enhanced Accuracy and Precision
3D modeling tools provide a high level of accuracy by allowing fabricators to create detailed and precise representations of metal components. The digital model can be manipulated and examined from various angles, ensuring that every detail is accounted for before the fabrication begins. - Reduced Errors and Rework
By visualizing the final product in a virtual environment, fabricators can identify potential issues early in the design process. This reduces the likelihood of errors and the need for costly rework. Any discrepancies can be addressed before the actual fabrication starts, saving time and resources. - Streamlined Communication and Collaboration
3D models can be easily shared with clients, engineers, and other stakeholders. This enhances communication and collaboration, as everyone involved can view and provide feedback on the design. This collaborative approach helps ensure that the final product meets all requirements and expectations. - Improved Efficiency and Productivity
With 3D modeling, fabricators can simulate the fabrication process and optimize workflows. This allows for better planning and resource allocation, leading to increased efficiency and productivity. Fabricators can also test different design iterations quickly, reducing the time required for prototyping. - Enhanced Visualization and Presentation
3D models offer a realistic and interactive representation of the final product. This can be particularly useful for presentations and client approvals, as it provides a clear and detailed view of the design. Clients can better understand the end result and provide more informed feedback.
How 3D Modeling Tools Work
1. Designing the 3D Model
The first step in using 3D modeling tools is to create a digital representation of the metal component or assembly. This is done using specialized software, such as SolidWorks, AutoCAD, or CATIA. The software allows fabricators to input precise measurements and specifications, creating an accurate 3D model of the design.
2. Simulating the Fabrication Process
Once the 3D model is created, fabricators can simulate the fabrication process within the software. This includes evaluating how the metal will be cut, shaped, and assembled. The simulation helps identify any potential issues, such as interference between components or manufacturing constraints.
3. Generating Fabrication Instructions
After finalizing the 3D model and simulation, the software generates detailed fabrication instructions. These instructions guide the CNC machines or other fabrication equipment, ensuring that each part is produced according to the digital design. The instructions include information on cutting paths, material specifications, and other relevant details.
4. Monitoring and Adjusting
During the fabrication process, fabricators can monitor progress and make adjustments as needed. The 3D model serves as a reference, allowing fabricators to verify that the physical components match the digital design. If any discrepancies are found, adjustments can be made to ensure precision.
Real-World Applications of 3D Modeling in Metal Fabrication
Aerospace Industry
In the aerospace industry, precision is paramount due to the high safety and performance standards required. 3D modeling tools are used to design and manufacture critical components, such as aircraft wings and engine parts. The ability to visualize and test designs in a virtual environment helps ensure that these components meet strict tolerances and performance requirements.
Automotive Industry
The automotive industry relies heavily on metal fabrication for manufacturing various components, including chassis, engine parts, and body panels. 3D modeling tools allow automotive manufacturers to design and test components with high precision, resulting in improved performance and safety. The ability to quickly iterate on designs also accelerates the development process.
Construction and Infrastructure
In construction and infrastructure projects, metal fabrication is used for structural elements, such as beams, columns, and frameworks. 3D modeling tools help ensure that these components are manufactured to exact specifications, leading to better-fitting assemblies and reduced on-site adjustments. This contributes to overall project efficiency and quality.
The Future of 3D Modeling in Metal Fabrication
As technology continues to evolve, the role of 3D modeling in metal fabrication is likely to expand further. Advances in software capabilities, hardware, and integration with other technologies (such as augmented reality and artificial intelligence) will continue to enhance precision and efficiency in the industry.
Integration with Augmented Reality
Augmented reality (AR) is an emerging technology that can complement 3D modeling tools. By overlaying digital models onto the physical world, AR can provide real-time guidance during the fabrication process. This can help fabricators visualize complex assemblies and identify potential issues more effectively.
Artificial Intelligence and Machine Learning
Artificial intelligence (AI) and machine learning have the potential to revolutionize metal fabrication by providing advanced analytics and optimization. These technologies can analyze data from 3D models and fabrication processes to predict and prevent issues, further enhancing precision and efficiency.
Conclusion
3D modeling in metal fabrication represents a significant advancement in achieving precision and efficiency in the industry. By allowing fabricators to design, visualize, and simulate metal components in a virtual environment, 3D modeling tools help reduce errors, improve communication, and streamline the fabrication process. As technology continues to advance, the role of 3D modeling will likely become even more integral to the future of metal fabrication.
For companies in Atmore AL and beyond, investing in advanced 3D modeling tools and precision equipment can provide a competitive edge and contribute to overall success in the metal fabrication industry.
Need a Machine Shop in Atmore, AL?
Escofab Inc. has been dedicated to providing quality machining and fabrication since 1981! Here at Escofab Inc. we utilize fabricating and machining to your specifications. We work to fit your needs and ensure customer satisfaction. Our friendly and informative staff are eager to assist you! Give us a call or come on in today; walk-ins welcome!