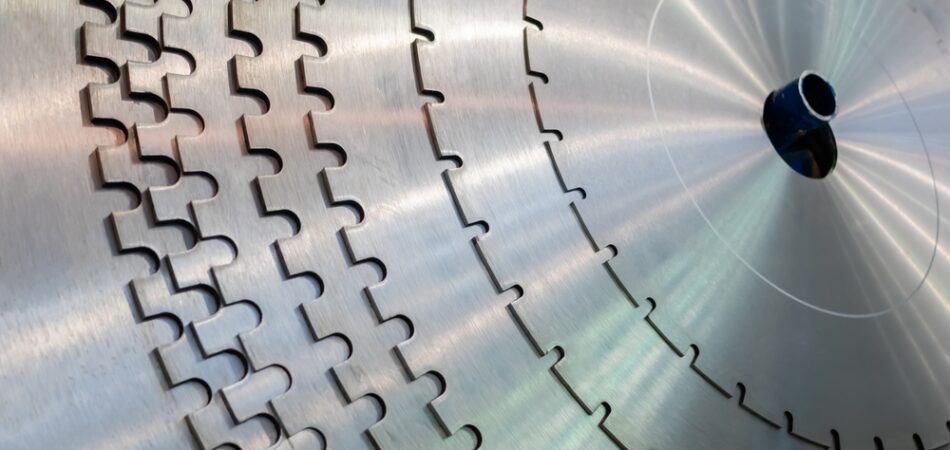
The world of manufacturing is rapidly evolving, and advanced CNC (Computer Numerical Control) machining is at the forefront of this transformation. With increasing automation, precision, and efficiency, CNC machining is integral to industries ranging from aerospace to medical devices. As technology progresses, the future of advanced CNC machining promises to be even more dynamic. This blog explores The Future of Advanced CNC Machining and delves into the Trends and Technologies to Watch in CNC Machining that are set to revolutionize the industry.
The Growing Importance of CNC Machining in Modern Manufacturing
CNC machining has been a cornerstone of modern manufacturing for decades. It involves the use of computer-controlled machines to precisely shape parts and components from raw materials. Traditional CNC processes have delivered significant improvements in precision, repeatability, and speed, making them indispensable in high-stakes industries like automotive, aerospace, and electronics.
As industries continue to demand higher quality, faster production times, and more cost-effective manufacturing processes, CNC machining is evolving. The future of advanced CNC machining is expected to incorporate cutting-edge technologies that will redefine what is possible in terms of efficiency and complexity.
Key Trends Shaping the Future of CNC Machining
To stay competitive in a fast-evolving market, manufacturers must be aware of the trends shaping the future of advanced CNC machining. Below are some of the most influential trends and technologies to watch in CNC machining that are expected to lead the charge.
1. Industry 4.0 and the Integration of Smart Manufacturing
One of the most significant trends influencing the future of advanced CNC machining is the shift towards Industry 4.0. This movement focuses on the digitalization and automation of manufacturing processes, creating “smart factories” where machines, systems, and humans communicate seamlessly.
In the context of CNC machining, Industry 4.0 enables real-time data collection and analytics, improving decision-making and optimizing machine performance. CNC machines equipped with IoT (Internet of Things) sensors can monitor key parameters like temperature, vibration, and tool wear, enabling predictive maintenance and reducing downtime. This minimizes production halts due to unexpected machine failures, making the entire manufacturing process more efficient.
Additionally, advanced software systems integrated with CNC machining will allow manufacturers to create digital twins of their production environments. These virtual models provide real-time insights and simulations of the entire production process, enabling manufacturers to detect inefficiencies and experiment with different scenarios without risking costly mistakes.
2. Additive Manufacturing Integration
Additive manufacturing (or 3D printing) is increasingly being integrated with traditional CNC machining to enhance flexibility and precision. While CNC machining is highly effective for subtractive manufacturing (removing material from a workpiece), additive manufacturing allows for the layer-by-layer building of complex geometries.
By combining these two methods, manufacturers can achieve unprecedented design freedom. CNC machines can be used to create the basic structure of a part, while additive manufacturing can add intricate features, such as internal channels, that would be impossible to machine using traditional methods. This hybrid approach reduces waste, speeds up production, and expands the range of parts that can be produced.
Moreover, additive manufacturing can be employed to create custom tooling for CNC machines, further enhancing efficiency and reducing lead times for specialized components.
3. Multi-Axis CNC Machining
Multi-axis machining is a growing trend in the CNC machining world that enables greater precision and complexity in the parts produced. While traditional CNC machines typically operate on three axes (X, Y, and Z), advanced machines can operate on five or more axes, allowing the machine to approach the workpiece from multiple angles.
This capability is especially valuable in industries like aerospace and medical devices, where complex, high-precision parts are often required. Multi-axis CNC machining enables the production of these parts in a single setup, reducing the need for multiple machine passes and improving both accuracy and efficiency.
As demand for intricate and precise parts increases, 5-axis and even 7-axis CNC machines are becoming more common. The future of advanced CNC machining will likely see further developments in multi-axis capabilities, opening up new possibilities for part design and reducing production time.
4. AI and Machine Learning in CNC Machining
The integration of artificial intelligence (AI) and machine learning (ML) is one of the most exciting trends shaping the future of CNC machining. AI can analyze vast amounts of data from machining processes to identify patterns and optimize performance. For example, AI can predict tool wear and adjust cutting speeds to prevent tool failure, reducing downtime and extending the lifespan of expensive equipment.
Machine learning algorithms can also enhance the programming of CNC machines. Rather than relying solely on human operators to define tool paths and machining strategies, ML algorithms can optimize these processes based on previous data, improving efficiency and reducing errors. This also opens the door to fully automated CNC machining, where machines can autonomously adjust their operations to achieve the best results with minimal human intervention.
5. Automation and Robotics
The push toward automation is transforming CNC machining, especially in industries that require high volumes of production with stringent quality standards. Robotics are increasingly being integrated with CNC systems to streamline workflows. Robotic arms can automatically load and unload workpieces, enhancing productivity by enabling 24/7 operation without the need for human oversight.
Furthermore, the integration of collaborative robots (cobots) allows CNC machines to work alongside human operators safely. These robots assist with repetitive or hazardous tasks, enabling human workers to focus on more complex and creative aspects of the production process. This combination of robotics and human oversight is paving the way for smarter, more flexible manufacturing environments.
6. Advances in Cutting Tools and Materials
The materials used in CNC machining are also evolving, driven by advancements in cutting tool technology and the development of new materials. For example, ceramic tools and diamond-coated tools offer superior durability and heat resistance, making them ideal for high-speed cutting applications. These tools can operate at higher temperatures and cutting speeds than traditional carbide tools, reducing cycle times and improving tool life.
In addition, superalloys and composite materials are becoming more common in industries such as aerospace and automotive, where lightweight and high-strength materials are essential. As the demand for these materials grows, CNC machines are being designed to handle more challenging machining processes, further expanding the range of applications in which CNC machining can be employed.
Challenges and Opportunities Ahead
While the future of advanced CNC machining is full of promise, it also presents several challenges. The rapid pace of technological development means that manufacturers need to continuously invest in new equipment, software, and training to stay competitive. There is also the issue of the skills gap in CNC machining, as many workers lack the expertise needed to operate increasingly complex machines.
However, these challenges also present opportunities. As CNC machining becomes more automated and intelligent, manufacturers can reduce their reliance on manual labor, lowering costs and improving consistency. Furthermore, advancements in machine learning and AI will simplify the programming of CNC machines, making the technology more accessible to a broader range of industries.
Conclusion
The future of advanced CNC machining is set to be shaped by a combination of emerging trends and technologies. From Industry 4.0 and multi-axis machining to the integration of AI and robotics, the potential for innovation in CNC machining is vast. These trends and technologies to watch in CNC machining will enable manufacturers to produce more complex, high-quality parts with greater efficiency and precision.
As CNC machining continues to evolve, it will play a critical role in transforming the manufacturing landscape. Those who embrace these advancements will be well-positioned to lead in the competitive world of modern manufacturing, driving productivity and innovation for years to come.
Need a Machine Shop in Atmore, AL?
Escofab Inc. has been dedicated to providing quality machining and fabrication since 1981! Here at Escofab Inc. we utilize fabricating and machining to your specifications. We work to fit your needs and ensure customer satisfaction. Our friendly and informative staff are eager to assist you! Give us a call or come on in today; walk-ins welcome!