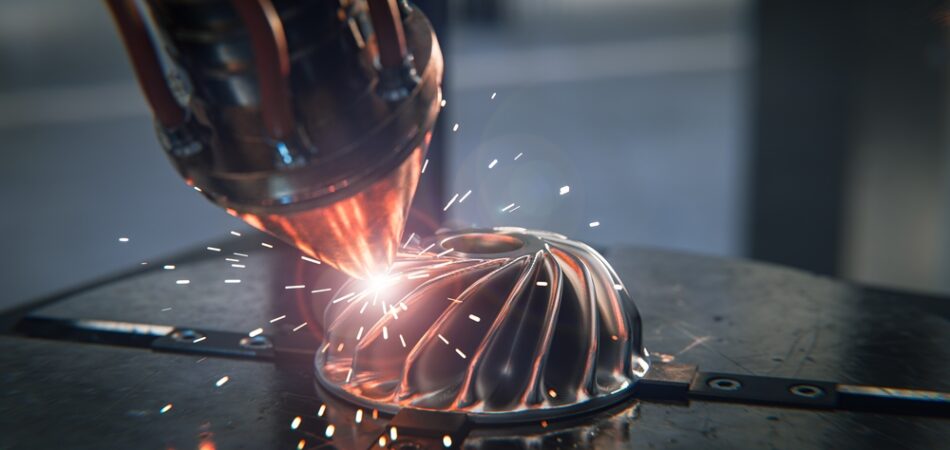
In recent years, 3D printing has shifted from a novel technology for prototyping into a transformative tool with profound implications for industrial manufacturing. Among the various materials that can now be 3D printed, metal stands out as a game-changer for industries from aerospace to automotive. With advancements in 3D metal printing technologies, businesses are tapping into the enormous potential this technology offers for innovation, efficiency, and cost reduction. This blog explores the emerging role of 3D metal printing in industrial applications, examining its benefits, technological innovations, and the cost savings it brings to the table.
The Rise of 3D Printing in Industrial Manufacturing
3D printing, also known as additive manufacturing, started primarily with polymers and plastics. However, as the technology matured, it became clear that printing in metals would open up a new range of possibilities, especially for high-performance industrial applications. Today, 3D metal printing is moving beyond prototyping and is increasingly used to manufacture functional parts for industries where precision and durability are critical.
3D printing for industrial applications is not only revolutionizing how products are designed and manufactured but also redefining supply chain dynamics, quality standards, and production timelines. With the ability to create intricate designs directly from digital models, manufacturers can bring complex products to life with unprecedented speed and precision.
Innovations in 3D Metal Printing: A Deep Dive
New Techniques in 3D Metal Printing
The evolution of 3D metal printing has introduced several techniques, each with its strengths, limitations, and ideal use cases. Some of the most innovative 3D metal printing techniques include:
- Selective Laser Melting (SLM): This technique uses high-powered lasers to fuse metal powder at precise locations, creating dense, durable metal parts. SLM is widely used for creating high-strength parts with intricate geometries, such as aerospace components.
- Electron Beam Melting (EBM): EBM utilizes electron beams instead of lasers to melt metal powder layers. It operates in a vacuum and is ideal for titanium and other reactive metals, commonly used in medical and aerospace applications.
- Binder Jetting: In binder jetting, a binding agent is deposited onto a bed of metal powder to build up parts layer by layer. It offers faster build speeds than laser-based methods and is popular for applications where high production rates are essential.
- Direct Metal Deposition (DMD): This technique involves melting metal wire or powder using a laser to create precise layers on a surface. DMD is suitable for repairs and adding material to existing parts, making it an ideal technique for maintenance and customizations.
These innovations in 3D metal printing technology empower manufacturers to select the best approach for their unique needs, from producing ultra-lightweight aerospace parts to creating customized medical implants.
Materials and Alloy Advancements
The range of metals and alloys available for 3D printing has expanded significantly, allowing for customizability to match application requirements. Materials commonly used in 3D metal printing include:
- Aluminum: Known for its lightweight properties, aluminum is widely used in automotive and aerospace industries.
- Titanium: Valued for its strength-to-weight ratio, titanium is crucial in medical and aerospace applications where biocompatibility and durability are paramount.
- Stainless Steel: Offering excellent corrosion resistance, stainless steel is popular for applications in harsh environments.
- Nickel Alloys: These are preferred for high-temperature applications, such as in jet engines and gas turbines.
By expanding the palette of materials suitable for 3D metal printing, manufacturers now have more options for meeting specific industry standards and performance needs.
The Benefits of 3D Printing in Metal Fabrication
3D metal printing offers several distinct advantages over traditional manufacturing processes, making it an attractive option for industrial applications. Here are some of the key benefits that set it apart:
Design Freedom and Customization
Traditional manufacturing methods often restrict the shapes and designs that can be created, as complex parts may require multiple machining steps or assembly from smaller components. 3D metal printing removes these constraints, enabling the fabrication of intricate geometries that would be impossible or highly costly to produce otherwise. This design freedom is crucial for industries like aerospace and medical, where unique, highly complex parts are in demand.
Rapid Prototyping and Reduced Lead Times
The ability to prototype quickly is one of the most significant advantages of 3D printing for industrial applications. By enabling rapid iteration, 3D metal printing shortens product development cycles and allows manufacturers to bring new products to market faster. Moreover, lead times can be drastically reduced, as the process often eliminates the need for tooling and setup time required in traditional manufacturing.
Cost Savings with 3D Metal Printing
One of the most compelling reasons for adopting 3D metal printing is the potential for cost savings. While the initial investment in 3D printing equipment can be significant, businesses can save on multiple fronts:
- Reduced Material Waste: Unlike subtractive manufacturing, which removes material to shape parts, additive manufacturing builds components layer by layer, minimizing waste. This reduction is particularly beneficial when working with expensive materials like titanium or nickel alloys.
- Lower Labor Costs: 3D printing is largely automated, requiring less manual labor and reducing associated costs.
- Inventory Savings: Since 3D printing allows on-demand production, companies can save on warehousing costs and reduce the need for large inventories, making supply chains more flexible and efficient.
Applications of 3D Metal Printing in Industry
Aerospace and Defense
The aerospace and defense sectors were among the earliest adopters of 3D metal printing. The technology enables the production of lightweight, complex parts that are strong enough to withstand extreme conditions. 3D printing allows for the creation of intricate fuel nozzles, brackets, and heat exchangers that contribute to aircraft efficiency and fuel savings. Defense contractors also benefit from rapid prototyping, which speeds up the development of advanced military equipment and allows for quick adjustments in the field.
Automotive Industry
In the automotive industry, 3D metal printing is being used to develop lightweight, durable components that enhance fuel efficiency and vehicle performance. The ability to create complex shapes without additional manufacturing steps enables designers to experiment with structures that were previously impossible to produce. From high-performance racing parts to custom luxury vehicle components, 3D metal printing is enhancing the way cars are designed and manufactured.
Medical Applications
3D printing has transformed the medical industry, particularly in creating personalized implants and prosthetics. With 3D metal printing, manufacturers can produce custom implants that fit a patient’s anatomy precisely, improving comfort and functionality. This personalization has applications across orthopedics, dental, and reconstructive surgery, where precision and biocompatibility are essential.
Energy and Power Generation
3D metal printing is also making significant contributions to the energy sector. Components for turbines, heat exchangers, and even parts for nuclear reactors are now being 3D printed to achieve designs that improve performance under high temperatures and pressures. The ability to produce parts with complex internal channels, such as cooling passages in turbine blades, makes 3D metal printing an ideal solution for power generation equipment.
The Challenges Facing 3D Metal Printing
While 3D metal printing is transforming industries, it also faces several challenges that must be addressed for widespread adoption:
- High Initial Costs: The upfront costs of 3D printing equipment can be a barrier for small and medium-sized enterprises, although the return on investment can be substantial in the long term.
- Material Limitations: Although the range of materials available for 3D printing is growing, certain materials remain challenging to print or are still in the research phase.
- Technical Expertise: Operating and maintaining 3D printing equipment requires specialized knowledge. Skilled professionals are essential to ensure high-quality production, which may increase labor costs.
The Future of 3D Metal Printing in Metal Fabrication
Despite these challenges, the future of 3D metal printing in metal fabrication is promising. As innovations in 3D metal printing continue to drive costs down and improve process efficiency, more industries are likely to adopt this technology. Advancements in machine learning, AI, and automation will further streamline 3D printing processes, making it possible to monitor and optimize manufacturing in real time.
In the coming years, the capabilities of 3D metal printing will expand to include even more materials and larger part sizes, unlocking new possibilities for metal fabrication. Moreover, as manufacturers gain experience and confidence in using 3D printing for high-stakes industrial applications, the technology will likely become an integral part of mainstream production.
Conclusion
3D printing in metal fabrication represents a new frontier in industrial manufacturing. From innovative techniques like selective laser melting and binder jetting to applications in aerospace, automotive, and medical fields, 3D metal printing is redefining the way industries think about production. With significant cost savings, rapid prototyping, and the ability to create highly customized parts, 3D metal printing is positioned to become a staple in the manufacturing toolkit. As technology advances and challenges are overcome, 3D metal printing will continue to unlock new opportunities for innovation and growth in industrial applications, making it an exciting time for the future of manufacturing.
Need a Machine Shop in Atmore, AL?
Escofab Inc. has been dedicated to providing quality machining and fabrication since 1981! Here at Escofab Inc. we utilize fabricating and machining to your specifications. We work to fit your needs and ensure customer satisfaction. Our friendly and informative staff are eager to assist you! Give us a call or come on in today; walk-ins welcome!