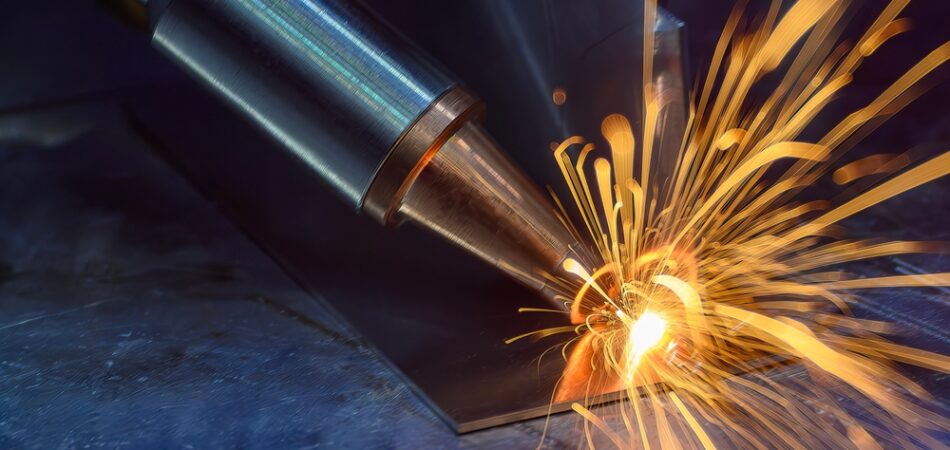
Welding is a critical component in many industries, from construction to manufacturing. However, without regular maintenance, welding equipment and techniques can deteriorate, leading to costly repairs and downtime. For businesses in Atmore, AL, prioritizing welding maintenance is a wise investment that can prevent unexpected expenses and ensure smooth operations.
In this blog, we’ll explore why welding maintenance is essential, how it can help prevent welding repairs in Atmore, and the steps you can take to establish a proactive maintenance routine.
The Importance of Welding Maintenance in Atmore, AL
Atmore’s industrial landscape thrives on reliable welding processes. Whether it’s for infrastructure projects, machinery fabrication, or routine repairs, welding plays an integral role. Yet, many companies overlook the need for regular maintenance until an issue arises.
Impact of Neglecting Welding Maintenance
When welding equipment isn’t properly maintained, problems can escalate, leading to:
- Inconsistent Weld Quality: Poorly maintained equipment can result in weak or faulty welds, compromising structural integrity.
- Increased Downtime: Equipment failures can halt production, leading to significant delays.
- Higher Repair Costs: Neglecting minor issues often results in major breakdowns, requiring expensive repairs or even replacement of machinery.
- Safety Hazards: Faulty welding equipment can create unsafe working conditions, endangering workers and increasing liability risks.
For businesses in Atmore, AL, these risks underscore the importance of a well-planned welding maintenance program.
Benefits of Regular Welding Maintenance
Investing time and resources in maintaining your welding equipment offers significant advantages. Here’s how regular maintenance can save you time, money, and stress:
1. Extends Equipment Lifespan
Welding machines are a substantial investment, and proper care ensures they last longer. Regular cleaning, inspection, and tune-ups prevent wear and tear, enabling your equipment to perform reliably over the years.
2. Reduces Downtime
Routine maintenance helps identify potential issues before they become major problems. By scheduling maintenance during non-peak hours, you can avoid unexpected downtime and keep your projects on track.
3. Ensures Consistent Quality
Clean and calibrated welding equipment produces consistent, high-quality welds. This is especially critical for businesses in Atmore, AL, where weld quality can directly impact structural safety and customer satisfaction.
4. Saves Money on Repairs
Preventative maintenance is far less expensive than emergency repairs or equipment replacement. By addressing small issues early, you can avoid costly repairs and operational disruptions.
5. Enhances Worker Safety
Faulty equipment can cause accidents, putting your team at risk. Regular inspections and repairs ensure your welding setup meets safety standards, reducing the likelihood of workplace injuries.
Common Welding Maintenance Practices
A well-rounded welding maintenance plan involves regular inspections, cleaning, and testing. Here are the key areas to focus on:
Inspection and Cleaning
- Check Electrical Connections: Loose or frayed cables can disrupt power flow and cause poor performance.
- Inspect Consumables: Replace worn-out nozzles, tips, and electrodes to ensure precise welds.
- Clean Welding Surfaces: Dirt and debris can interfere with weld quality. Clean work areas and surfaces before each job.
Equipment Calibration
Proper calibration ensures your equipment operates at the correct voltage, current, and speed. Test and adjust your machines periodically to maintain optimal performance.
Preventative Repairs
Identify and address small issues, such as worn cables or damaged components, during routine maintenance. This proactive approach prevents more extensive repairs down the line.
Lubrication
Ensure moving parts, such as wire feeders, are well-lubricated to reduce friction and wear.
Safety Checks
Regularly inspect safety equipment, including helmets, gloves, and ventilation systems, to protect workers from hazards.
How to Prevent Welding Repairs in Atmore, AL
Preventing welding repairs starts with adopting a proactive approach to equipment care. For businesses in Atmore, AL, here are practical steps to follow:
Create a Maintenance Schedule
Develop a detailed maintenance plan, outlining tasks to be completed daily, weekly, and monthly. Assign responsibilities to specific team members and track progress to ensure compliance.
Train Your Team
Proper equipment handling and maintenance require skilled workers. Provide regular training to ensure your team understands best practices for operating and maintaining welding machinery.
Partner with Professionals
Working with experienced welding technicians in Atmore, AL can provide valuable insights and assistance. These professionals can conduct detailed inspections, perform repairs, and offer expert advice on maintenance strategies.
Use Quality Materials
Invest in high-quality consumables and replacement parts to minimize wear and tear. Cutting corners with subpar materials can lead to frequent repairs and reduced efficiency.
Monitor Equipment Performance
Keep a log of equipment performance, noting any irregularities or recurring issues. This data can help identify patterns and prevent future problems.
Choosing the Right Welding Maintenance Partner in Atmore, AL
While some maintenance tasks can be handled in-house, partnering with a professional welding service provider ensures more comprehensive care. When choosing a partner in Atmore, AL, consider the following:
Experience and Expertise
Look for a provider with a proven track record in welding maintenance and repair. Experienced technicians can quickly identify issues and recommend effective solutions.
Customizable Services
Every business has unique needs. Choose a partner who offers tailored maintenance plans to suit your equipment, workload, and budget.
Quick Response Time
In case of unexpected issues, a responsive partner can minimize downtime. Ensure your provider offers reliable emergency repair services.
Commitment to Safety
Safety is paramount in welding operations. Partner with a provider who prioritizes safety and adheres to industry standards.
Case Study: Preventing Welding Repairs in Atmore, AL
Let’s consider a local business in Atmore, AL that implemented a proactive welding maintenance plan. A manufacturing company specializing in heavy machinery faced recurring downtime due to equipment malfunctions. By partnering with a welding maintenance provider, they established a regular inspection and servicing schedule.
The results were remarkable:
- Improved Productivity: Downtime was reduced by 30%, enabling the company to meet project deadlines more efficiently.
- Cost Savings: Preventative maintenance lowered repair costs by 40%, freeing up resources for other investments.
- Enhanced Safety: Regular safety checks reduced workplace accidents, boosting employee confidence and morale.
This case highlights the tangible benefits of investing in welding maintenance to prevent costly repairs.
Prioritize Welding Maintenance in Atmore, AL
Welding maintenance is not just a best practice—it’s a necessity for businesses in Atmore, AL. By prioritizing regular maintenance, you can prevent costly repairs, extend equipment lifespan, and ensure consistent quality and safety.
If you’re ready to take the next step, consider working with experienced welding professionals in Atmore who can help you develop and implement a comprehensive maintenance plan. Investing in preventative care today will pay dividends in the long run, saving you time, money, and stress.
Don’t wait until a breakdown disrupts your operations—start your welding maintenance journey today and see the difference it makes!
Need a Machine Shop in Atmore, AL?
Escofab Inc. has been dedicated to providing quality machining and fabrication since 1981! Here at Escofab Inc. we utilize fabricating and machining to your specifications. We work to fit your needs and ensure customer satisfaction. Our friendly and informative staff are eager to assist you! Give us a call or come on in today; walk-ins welcome!