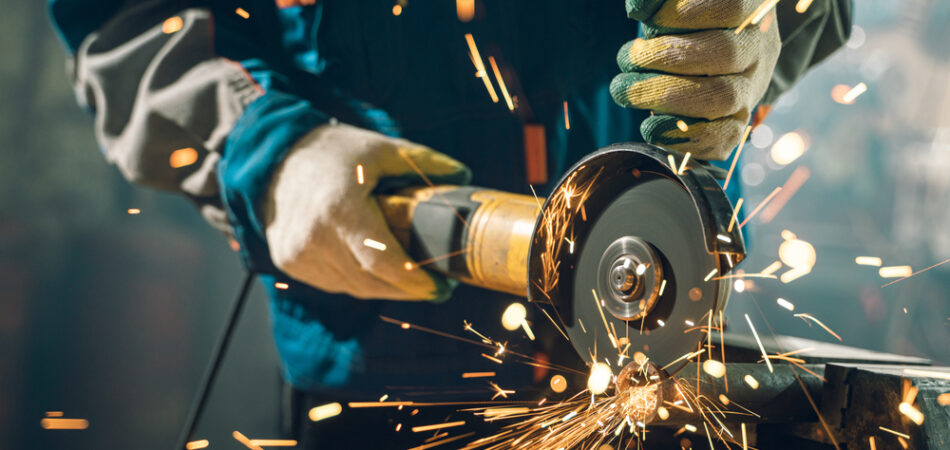
Welding is a fundamental process in the construction industry, serving as the backbone for building structures that must withstand immense loads and environmental pressures. The strength, durability, and integrity of buildings, bridges, and other infrastructure heavily depend on structural welding. When performed correctly, welding creates robust connections that ensure the stability of a structure for years to come. However, poor welding practices can lead to catastrophic failures, putting lives at risk and causing significant financial and reputational losses for construction companies. Welding safety is a critical aspect of the industry, as any lapse in quality can compromise an entire project. Therefore, maintaining high standards in welding is not just a matter of compliance but a crucial factor in ensuring long-term safety and reliability.
The Role of Skilled Welders in Structural Integrity
The effectiveness of structural welding largely depends on the skills and expertise of the welders involved. Proper training and experience enable welders to execute precise welds that meet industry standards and building codes. Skilled professionals understand the significance of factors such as material selection, heat control, and welding techniques, all of which contribute to the overall strength of a structure. Without these competencies, there is an increased likelihood of defects such as cracks, porosity, and weak joints, which can lead to structural failures.
Furthermore, welding safety encompasses not only the prevention of immediate hazards, such as burns and exposure to toxic fumes, but also the long-term stability of the welded structure. A skilled welder follows strict procedures to ensure that each weld is performed correctly and adheres to safety regulations. Construction projects that prioritize high-quality welding employ certified welders who have undergone rigorous training and testing, thereby reducing the risk of structural failures that could endanger workers and occupants alike.
Common Welding Defects and Their Consequences
Defective welding is one of the leading causes of structural failures in construction. Some of the most common welding defects include incomplete penetration, lack of fusion, slag inclusion, and porosity. These defects can significantly compromise the strength of a weld, leading to weaknesses that may not be immediately visible but can cause severe issues over time.
Incomplete penetration occurs when the weld metal does not fully penetrate the joint, creating a weak connection between the welded materials. Similarly, lack of fusion happens when the weld metal fails to fuse properly with the base material, leading to weak spots in the structure. Slag inclusion, on the other hand, results from impurities getting trapped within the weld, which can weaken the overall bond. Porosity, caused by trapped gases, creates small holes in the weld, reducing its load-bearing capacity.
These defects can have dire consequences, including structural collapses, equipment failures, and costly repairs. In large-scale construction projects, undetected welding defects can lead to catastrophic failures, endangering workers and the public. This is why regular inspections and adherence to strict quality control measures are essential to ensuring that all welds meet safety standards.
The Importance of Welding Safety Regulations
Welding safety regulations are put in place to protect workers and ensure the structural integrity of buildings and infrastructure. Regulatory bodies such as the American Welding Society (AWS) and the Occupational Safety and Health Administration (OSHA) have established guidelines that govern welding procedures, materials, and safety practices. These regulations mandate proper training, equipment use, and inspection protocols to prevent accidents and ensure the quality of welded structures.
Adhering to welding safety guidelines helps mitigate risks associated with improper welding practices. Proper ventilation, protective gear, and adherence to welding parameters such as temperature and welding speed are essential for preventing defects and ensuring high-quality welds. Additionally, non-destructive testing methods such as ultrasonic and radiographic testing allow for the detection of hidden defects that could compromise structural integrity.
Construction companies that prioritize welding safety not only protect their workers but also ensure the longevity and reliability of their projects. Failure to comply with safety regulations can result in legal consequences, project delays, and financial losses. Therefore, investing in training, quality control, and adherence to industry standards is crucial for achieving safe and durable structures.
The Future of Welding in Construction
Advancements in welding technology continue to enhance the quality and safety of construction projects. Automation and robotic welding systems are becoming increasingly popular, allowing for greater precision and consistency in welds. These technologies reduce the margin of error and minimize human exposure to hazardous welding environments, further improving welding safety.
Additionally, the development of new welding materials and techniques is leading to stronger and more efficient structural welding practices. Innovations such as laser welding and friction stir welding are revolutionizing the industry by offering improved strength and reduced heat distortion. These advancements contribute to the construction of safer, more durable structures while increasing efficiency and reducing costs.
Conclusion
As the construction industry continues to evolve, the demand for high-quality welding will only increase. Companies that invest in skilled labor, advanced technology, and strict quality control measures will set themselves apart as leaders in the industry. Prioritizing welding safety and quality not only ensures compliance with regulations but also safeguards lives and investments. Ultimately, quality welding is not just a technical requirement—it is a fundamental pillar of safety and success in construction.
Need a Machine Shop in Atmore, AL?
Escofab Inc. has been dedicated to providing quality machining and fabrication since 1981! Here at Escofab Inc. we utilize fabricating and machining to your specifications. We work to fit your needs and ensure customer satisfaction. Our friendly and informative staff are eager to assist you! Give us a call or come on in today; walk-ins welcome!