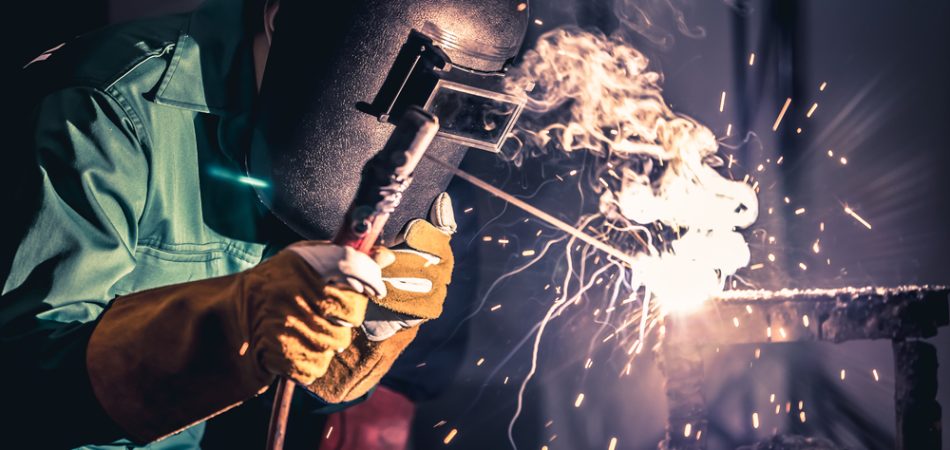
Welding, the process of joining materials permanently by fusion, is a critical technique in manufacturing, construction, and various industrial applications. One common query in welding is whether different metals can be welded together. This question arises due to the diverse properties and behaviors of metals when subjected to heat and pressure. Let’s delve into the intricacies of welding different metals together, exploring techniques, challenges, and considerations.
Welding and Metal Properties
Welding Fundamentals
Welding typically involves heating materials to their melting point or using pressure to create a strong joint. The aim is to achieve a bond that is as strong as the base materials themselves. Different welding methods exist, including arc welding, gas welding, and laser welding, each suitable for specific applications and materials.
Metallurgical Properties
Metals vary widely in their chemical composition, atomic structure, and physical properties such as melting point, thermal conductivity, and ductility. These properties influence how metals behave during welding and the feasibility of welding different metals together.
Challenges in Welding Different Metals
Compatibility Issues
One of the primary challenges in welding different metals is their compatibility. Metals with vastly different melting points, thermal expansion coefficients, or metallurgical structures may not weld together effectively. For instance, welding aluminum to steel is complex due to the significant differences in their properties.
Metallurgical Considerations
When different metals are welded together, the welded joint experiences a zone where the properties of both metals interact. This fusion zone can have varying mechanical properties compared to the base metals, affecting the overall strength and integrity of the joint.
Techniques for Welding Different Metals
Mechanical Fastening
In cases where welding different metals is impractical or challenging, mechanical fastening techniques such as riveting or bolting can be employed. These methods provide a secure connection without the need for metallurgical fusion.
Intermediate Layers
Using intermediate layers of compatible metals or alloys can facilitate welding between dissimilar metals. These layers act as a bridge, reducing the direct interaction between the base metals and improving the weldability of dissimilar combinations.
Specialized Welding Processes
Certain specialized welding processes, such as explosion welding or friction welding, can join dissimilar metals effectively. These methods utilize high energy input to create bonds at the interface of different metals, overcoming some of the challenges encountered with traditional welding techniques.
Examples of Welding Different Metals
Aluminum and Steel
Welding aluminum to steel is notoriously difficult due to the stark contrast in their properties. Techniques like friction stir welding or using intermediary materials like aluminum-silicon alloys can enhance the feasibility of creating strong joints between these metals.
Stainless Steel and Carbon Steel
Stainless steel and carbon steel can be welded together using appropriate welding techniques and filler materials. However, careful consideration must be given to prevent issues such as intermetallic phases or corrosion susceptibility in the welded joint.
Considerations for Successful Welding
Material Preparation
Successful welding of different metals requires thorough material preparation, including cleaning, surface treatment, and proper fit-up. Contaminants such as oils, oxides, or coatings can impair the quality of the weld joint.
Welding Parameters
Optimizing welding parameters such as heat input, welding speed, and shielding gas composition is crucial when welding dissimilar metals. These parameters influence the microstructure and mechanical properties of the welded joint.
Post-Welding Treatment
Post-welding treatments such as stress relieving or heat treatment may be necessary to improve the mechanical properties and durability of the welded joint, especially when welding dissimilar metals.
Applications of Welding Different Metals
Aerospace Industry
In aerospace applications, welding different metals is common to achieve lightweight structures with high strength. Techniques like electron beam welding or laser welding are employed to join aluminum alloys, titanium alloys, and steels.
Automotive Industry
The automotive industry utilizes welding to join dissimilar metals in components such as chassis, engine parts, and body panels. Hybrid materials like aluminum-steel or magnesium-aluminum alloys are welded to meet performance and weight reduction targets.
Conclusion
Welding different metals together is feasible with the right techniques, considerations, and expertise. While challenges such as metallurgical incompatibility or mechanical properties variation exist, advancements in welding technology and materials science continue to expand the possibilities. Understanding the properties of metals, selecting appropriate welding methods, and meticulous execution are key to achieving strong and reliable weld joints between dissimilar metals. As industries evolve and demand for complex material combinations grows, the role of welding in joining different metals will remain pivotal in manufacturing and construction sectors worldwide.
Need a Machine Shop in Atmore, AL?
Escofab Inc. has been dedicated to providing quality machining and fabrication since 1981! Here at Escofab Inc. we utilize fabricating and machining to your specifications. We work to fit your needs and ensure customer satisfaction. Our friendly and informative staff are eager to assist you! Give us a call or come on in today; walk-ins welcome!