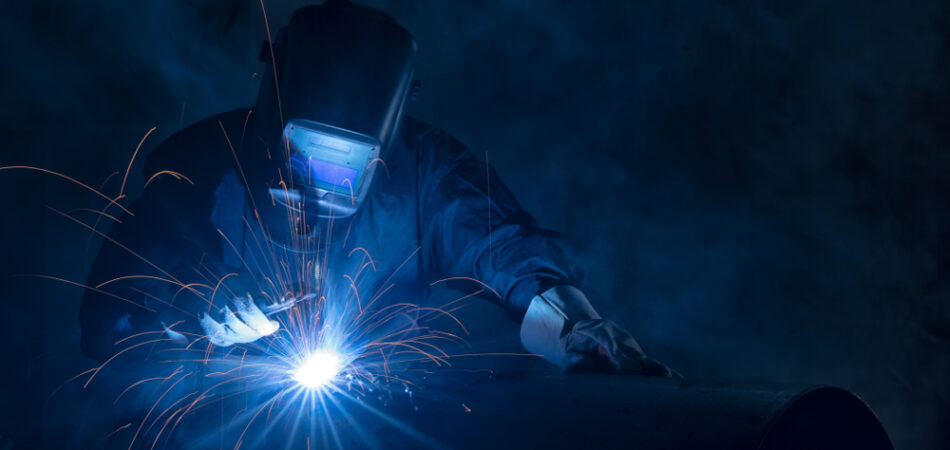
Welding is a critical process in industries ranging from construction to manufacturing. However, it involves risks such as fire hazards, toxic fumes, and UV radiation, making safety a top priority. This blog provides a detailed guide on how to improve welding safety by implementing comprehensive safety protocols and procedures.
Why Welding Safety Is Crucial
Safety in welding is not just about compliance with regulations; it’s about protecting lives and maintaining productivity. Unsafe practices can lead to severe injuries, property damage, and costly downtime. Implementing welding safety procedures ensures that workers operate in a secure environment and reduces the likelihood of accidents.
Common Welding Hazards
- Fire and Explosion Risks
Sparks and heat generated during welding can ignite flammable materials. - Toxic Fumes and Gases
Welding produces fumes that can harm respiratory health if inhaled over time. - Electrical Hazards
The use of electric arcs poses risks of shock or electrocution. - Radiation Exposure
UV and infrared radiation can cause eye injuries and skin burns. - Physical Injuries
Improper handling of equipment and materials can lead to burns, cuts, or musculoskeletal injuries.
Understanding these hazards is the first step toward implementing effective safety protocols.
Steps to Implement Welding Safety Procedures
Ensuring safety in welding projects requires a systematic approach. Here are key steps to create and enforce safety protocols:
Assessing Workplace Hazards
Conduct a thorough hazard assessment before starting any welding project. Identify risks related to the workspace, materials, and equipment.
- Inspect the Environment: Ensure adequate ventilation, remove flammable materials, and secure loose items.
- Evaluate Equipment: Check for wear and tear on welding machines, cables, and protective gear.
- Assess Worker Preparedness: Verify that workers are trained and aware of potential hazards.
Developing a Welding Safety Plan
A well-documented safety plan is essential for large-scale or high-risk welding projects. It should include:
- Detailed Risk Assessment: Outline specific hazards and mitigation measures.
- Clear Safety Guidelines: Describe steps for safe operation of equipment and emergency procedures.
- Roles and Responsibilities: Assign accountability for implementing safety measures.
Training and Certification
Proper training is a cornerstone of safe welding practices. Workers should undergo formal training that covers:
- Operating Welding Equipment: Understanding machine functions and limitations.
- Using Personal Protective Equipment (PPE): Emphasizing the importance of helmets, gloves, and fire-resistant clothing.
- Emergency Response Skills: Teaching first-aid basics and how to handle fire or toxic exposure incidents.
Certifications from recognized organizations, such as the American Welding Society (AWS), further validate a welder’s skills and safety awareness.
Essential Safety Equipment for Welding
Investing in the right protective gear and tools significantly enhances safety during welding projects.
Personal Protective Equipment (PPE)
- Welding Helmets
Equipped with auto-darkening filters to protect against UV and infrared radiation. - Gloves and Aprons
Heat-resistant materials shield hands and body from sparks and hot metal. - Respirators
Necessary for projects involving hazardous fumes or inadequate ventilation. - Safety Glasses and Ear Protection
Shield eyes from debris and ears from high noise levels.
Worksite Safety Tools
- Fire Extinguishers: Place them strategically for quick access.
- Ventilation Systems: Ensure proper air circulation to disperse toxic fumes.
- Insulated Tools: Prevent electrical hazards.
Enforcing Safety Protocols
Having a safety plan is not enough; enforcement is critical. Here’s how to ensure compliance:
Regular Inspections and Maintenance
- Conduct routine checks on equipment and PPE.
- Replace worn or damaged gear promptly.
- Schedule periodic audits of the workspace to identify and mitigate new risks.
Promoting a Culture of Safety
A proactive safety culture ensures that everyone prioritizes welding safety. Encourage open communication where workers can report hazards without fear of reprisal.
Using Checklists
Develop checklists for daily safety routines, such as inspecting equipment, verifying PPE use, and reviewing emergency procedures. These checklists standardize practices and reduce oversight.
The Role of Technology in Welding Safety
Advancements in technology offer new ways to improve welding safety. Tools like automated welding machines and monitoring systems can reduce human error and enhance overall safety.
Automated Welding Machines
Automated systems minimize the need for manual handling, reducing exposure to hazards. These machines are especially useful for repetitive tasks or dangerous environments.
Real-Time Monitoring Systems
Wearable sensors and connected devices can track environmental conditions, worker health, and equipment performance, providing actionable insights to improve safety protocols.
Emergency Preparedness in Welding
Despite all precautions, emergencies can still occur. Preparation is vital to mitigate damage and ensure worker safety.
Developing an Emergency Response Plan
- Identify Potential Scenarios: Consider fires, gas leaks, and electrical failures.
- Establish Clear Procedures: Assign evacuation routes, assembly points, and first-aid responsibilities.
- Conduct Drills: Regular practice ensures everyone knows their role in an emergency.
Stocking Emergency Supplies
Keep the following on hand:
- First-aid kits
- Fire extinguishers
- Eye wash stations
Continuous Improvement in Welding Safety
Safety is an ongoing process. Regularly updating protocols and procedures ensures they remain effective as technologies and work environments evolve.
Collecting Feedback
Encourage workers to share insights and suggestions for improving safety measures. Their firsthand experience can highlight overlooked issues.
Reviewing Incident Reports
Analyze past accidents to identify patterns and areas for improvement. Use these findings to refine safety protocols.
Staying Updated on Industry Standards
Compliance with regulations like OSHA standards is non-negotiable. Monitor updates to industry guidelines and incorporate best practices into your safety plan.
Conclusion
Implementing welding safety procedures requires a combination of proactive planning, rigorous training, and regular enforcement. By investing in protective equipment, fostering a culture of safety, and leveraging modern technologies, you can significantly reduce risks and create a safer work environment.
Understanding how to improve welding safety not only protects your team but also enhances project efficiency and quality. Safety is not just a regulatory requirement—it is a commitment to excellence and responsibility in every welding project.
Need a Machine Shop in Atmore, AL?
Escofab Inc. has been dedicated to providing quality machining and fabrication since 1981! Here at Escofab Inc. we utilize fabricating and machining to your specifications. We work to fit your needs and ensure customer satisfaction. Our friendly and informative staff are eager to assist you! Give us a call or come on in today; walk-ins welcome!