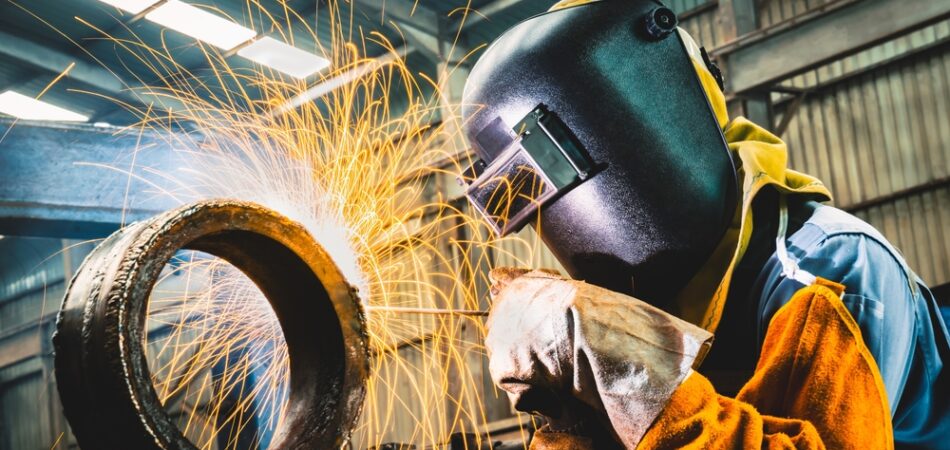
Industrial welding is a cornerstone in the world of manufacturing and construction, offering the essential bond between various metal components to create strong, durable structures. From large-scale industrial projects to custom metal fabrication, welding plays an indispensable role in ensuring the functionality, safety, and longevity of heavy-duty applications. Whether it’s building steel frames for skyscrapers, crafting heavy machinery, or repairing intricate parts for industrial equipment, industrial welding services ensure that these projects hold up under immense pressure and harsh conditions. This blog will explore the significance of industrial welding, its applications, and how it contributes to the strength and durability of heavy-duty projects.
The Importance of Industrial Welding in Manufacturing and Construction
In the realm of manufacturing and construction, industrial welding is not just a process but a vital service that ties together raw materials to form finished products. Welding connects metal parts permanently by using high heat to melt the materials and fuse them together, creating a bond that’s often stronger than the original material itself. This is particularly important in heavy-duty applications where strength and durability are paramount. The ability to weld metals with precision ensures that even the most complex designs can be achieved while maintaining structural integrity.
One of the key reasons industrial welding is so important in these sectors is the wide variety of metals and materials that are used. In manufacturing, industries utilize everything from carbon steel to stainless steel, aluminum, and even exotic alloys like titanium. Industrial welding services are crucial for connecting these materials in ways that achieve the desired structural characteristics, such as strength, flexibility, and corrosion resistance. A well-executed weld not only provides a solid connection but also ensures that the metal components can withstand the stresses they will encounter throughout their service life.
Furthermore, industrial welding offers significant benefits when it comes to cost-effectiveness and time efficiency. In large-scale projects, using welding techniques such as arc welding, MIG (Metal Inert Gas) welding, or TIG (Tungsten Inert Gas) welding allows for faster assembly compared to other methods like bolting or riveting. This reduces both labor costs and the time required to complete a project, without compromising on the quality of the final result.
Custom Metal Fabrication: Tailoring Solutions for Specialized Needs
Custom metal fabrication is another critical aspect of industrial welding services that is essential for creating bespoke solutions to meet the specific needs of heavy-duty applications. Whether it’s a complex part for a custom machine or a unique structural component for a construction project, custom metal fabrication allows for the creation of highly specialized metal parts that fit perfectly within a given design or function.
One of the primary benefits of custom metal fabrication is its ability to create parts with exact specifications, which is particularly important in industries that demand precision, such as aerospace, automotive, and energy. Custom fabrication can involve a range of processes, including welding, cutting, bending, and machining, to produce the final product. For example, when creating custom parts for a machine, welding allows different metal pieces to be joined together in a way that ensures the parts are strong, aligned, and able to endure harsh operational conditions.
In many instances, custom metal fabrication is necessary for parts that aren’t readily available through standard manufacturing channels. When a specialized project requires a part that doesn’t exist in mass production, a metal fabrication shop will often step in to design and fabricate the exact piece needed. This is especially true for the maintenance of industrial equipment, where worn-out components need to be replaced with custom-fabricated parts that match the original specifications perfectly. Whether it’s producing complex components for machinery or creating custom-designed frames for heavy equipment, custom metal fabrication ensures that industrial projects are completed to precise standards.
Heavy-Duty Applications That Rely on Industrial Welding
Industrial welding is integral to a variety of heavy-duty applications, each with its own unique challenges and demands. These industries rely on the strength and precision of welded joints to ensure that their projects meet safety standards, perform as expected, and endure the harshest conditions.
One of the most significant industries that depend on industrial welding services is the construction industry. Welding is essential for creating steel frameworks, structural beams, and reinforcing bars for buildings and bridges. These structures must support substantial loads, and the welds must be robust enough to handle the stresses over the building’s entire lifespan. In particular, high-rise buildings and bridges require welding techniques that offer maximum strength and resistance to environmental factors, such as wind, seismic activity, and temperature fluctuations.
Similarly, the oil and gas industry uses industrial welding to construct pipelines and offshore platforms. These projects are exposed to extreme conditions, including high pressures, corrosive environments, and heavy machinery. The welds created in such projects must withstand not only the mechanical stress of the equipment but also the challenges posed by harsh weather, saltwater corrosion, and fluctuating temperatures. Welding ensures that pipelines are properly sealed, and platforms remain structurally sound, preventing catastrophic failures.
The transportation sector also relies on industrial welding for the creation of vehicles, railways, and other transportation infrastructure. Heavy-duty trucks, rail cars, and even aircraft require strong, reliable welds to keep the vehicles in service under harsh operating conditions. Whether it’s a massive cargo ship or a high-speed train, the integrity of the welds ensures that these vehicles are safe, efficient, and capable of handling heavy loads without failure.
The Role of Technology in Advancing Industrial Welding
As industrial welding continues to play a pivotal role in various heavy-duty applications, technology is enhancing the capabilities and precision of welding techniques. The integration of advanced technologies into welding services is improving the overall efficiency, safety, and quality of welded structures. Robotic welding, automated systems, and digital monitoring tools are revolutionizing the way industrial welding is performed.
Robotic welding, in particular, has transformed the manufacturing landscape by providing precision and consistency that is difficult to achieve with manual methods. Robots can perform repetitive welding tasks at high speeds, ensuring uniform welds and reducing the margin for error. In high-volume industries, robotic welding is particularly beneficial because it can work around the clock, increasing production rates while maintaining high levels of quality control.
Automated welding systems, equipped with sensors and real-time monitoring capabilities, provide welders with precise data to make immediate adjustments to welding parameters. This results in fewer defects, reduced waste, and a higher level of craftsmanship in the final product. Digital tools are also used to simulate welding processes before they are executed in the real world, allowing for the optimization of welding designs and minimizing trial and error.
Moreover, advancements in welding materials and techniques have led to the development of stronger, more durable welds. For instance, the advent of high-strength alloys and specialized welding rods has enabled the creation of stronger welds that can endure extreme conditions, such as those found in the aerospace and automotive industries. These technological innovations ensure that industrial welding continues to meet the evolving needs of heavy-duty applications and contributes to the overall success of complex projects.
Quality Assurance and Safety in Industrial Welding
The importance of quality assurance and safety in industrial welding cannot be overstated. Given that industrial welding often takes place in hazardous environments or on critical infrastructure, ensuring the highest standards of quality is essential to prevent failures that could result in significant financial losses, environmental damage, or even human injury. To achieve this, welding service providers adhere to strict industry standards and employ rigorous testing and inspection methods throughout the welding process.
Quality assurance in industrial welding involves numerous processes, such as non-destructive testing (NDT), to verify the integrity of welded joints without causing any damage. Techniques like ultrasonic testing, radiographic testing, and magnetic particle testing allow for the detection of flaws in the welds, such as cracks, voids, or incomplete fusion, ensuring that only the highest-quality welds are approved. These tests are critical in industries like aerospace, defense, and oil and gas, where even a minor defect could have catastrophic consequences.
Additionally, safety is paramount in industrial welding due to the high-risk nature of the work. Welders are exposed to intense heat, ultraviolet radiation, and potentially hazardous fumes. Protective gear such as welding helmets, gloves, and respirators is crucial to safeguard workers’ health. Furthermore, industrial welding operations are typically conducted in compliance with occupational safety standards, ensuring that all welding activities are performed in a controlled, secure environment. Welding service providers invest in training and safety protocols to protect both workers and the integrity of the projects being completed.
Conclusion
Industrial welding services are essential in ensuring the strength, durability, and safety of heavy-duty applications across numerous industries. By combining the precision of welding with advanced technologies, custom metal fabrication, and rigorous safety standards, industrial welding continues to play a critical role in the construction, manufacturing, and maintenance of some of the most demanding structures and equipment in the world. Whether it’s for custom projects or large-scale infrastructure, industrial welding services are the backbone that ensures the resilience and longevity of essential industries.
Need a Machine Shop in Atmore, AL?
Escofab Inc. has been dedicated to providing quality machining and fabrication since 1981! Here at Escofab Inc. we utilize fabricating and machining to your specifications. We work to fit your needs and ensure customer satisfaction. Our friendly and informative staff are eager to assist you! Give us a call or come on in today; walk-ins welcome!