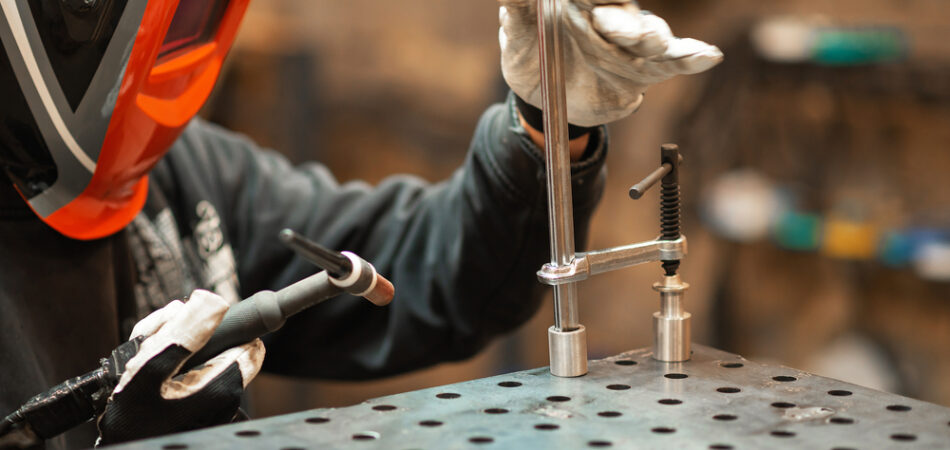
In the industrial sector, precision, durability, and efficiency are paramount. The right welding solutions play a critical role in ensuring that infrastructure, machinery, and components meet the rigorous demands of modern industries. Industrial welding services are evolving rapidly, offering customized approaches tailored to the specific requirements of diverse industries. In this blog, we delve into the key advantages of custom welding solutions for industrial needs and highlight why specialized fabrication welding has become a game-changer.
Understanding Custom Welding Solutions
Custom welding solutions go beyond the standard one-size-fits-all approach. They are designed to address unique challenges, ensuring that the final product aligns precisely with the client’s specifications. These solutions are particularly beneficial in industries like construction, automotive, aerospace, energy, and manufacturing, where precision and specialized materials are critical.
What Makes Custom Welding Different?
- Tailored Design: Custom welding focuses on creating solutions that fit unique design and operational requirements.
- Specialized Materials: It allows for the use of materials that best suit the specific application, such as stainless steel, aluminum, or exotic alloys.
- Enhanced Techniques: Advanced welding methods like TIG, MIG, and robotic welding are employed to achieve superior results.
Advantages of Custom Welding Solutions
1. Precision and Accuracy
Custom welding services ensure that components and structures meet exact specifications. This level of precision is essential for industries that rely on seamless integration and flawless performance. For instance, in aerospace engineering, even the slightest deviation can compromise safety and functionality.
Specialized fabrication welding ensures:
- Accurate measurements
- Perfect alignment of parts
- High-quality joints that withstand stress
2. Versatility in Applications
Industries have diverse requirements, from constructing heavy machinery to creating intricate components. Custom welding caters to this diversity by offering solutions tailored to various applications. Whether it’s large-scale structural welding for construction or fine-detail work for medical devices, custom welding services adapt to the task at hand.
Key areas of application include:
- Industrial Machinery: Building and repairing critical machine parts
- Construction: Fabrication of beams, columns, and structural supports
- Automotive: High-performance welding for chassis and body parts
3. Use of Advanced Technology
The integration of cutting-edge technology in custom welding enhances productivity and quality. Robotic welding systems, for example, ensure consistency and precision in repetitive tasks. This is particularly beneficial for large-scale production environments, where human error could lead to costly defects.
Technological advancements in industrial welding services include:
- Laser welding for fine precision
- Computer-aided design (CAD) integration for exact specifications
- Automated inspection systems for quality assurance
4. Cost-Effectiveness
While custom welding might seem more expensive initially, it often results in long-term cost savings. By providing precisely what is needed, it minimizes waste, reduces material costs, and enhances durability, leading to fewer repairs and replacements over time.
Cost benefits of specialized fabrication welding include:
- Reduced material wastage
- Longer lifespan of welded components
- Lower maintenance costs
5. Enhanced Durability and Strength
Industries often operate in extreme conditions, requiring components that can endure stress, high temperatures, and corrosive environments. Custom welding solutions ensure that the materials and techniques used are best suited to withstand these challenges, enhancing the longevity and reliability of the final product.
For example:
- Oil and Gas: High-strength welding to endure pressure and temperature variations
- Marine: Corrosion-resistant welding for saltwater environments
6. Compliance with Industry Standards
Custom welding services adhere to strict industry standards, ensuring safety and reliability. This is especially critical in sectors like aerospace and energy, where regulatory compliance is non-negotiable. Professional welders are well-versed in certifications and standards such as ASME, AWS, and ISO, providing clients with confidence in the quality of their work.
The Role of Specialized Fabrication Welding
Specialized fabrication welding is an integral part of custom welding solutions. It involves creating complex structures and components from raw materials, tailored to meet specific industrial demands. This approach combines craftsmanship with advanced techniques to produce superior results.
Why Choose Specialized Fabrication Welding?
- Complex Designs: Ideal for projects requiring intricate or unconventional designs.
- Material Expertise: Skilled fabricators work with a wide range of metals, ensuring compatibility and performance.
- Precision Techniques: Techniques like TIG and MIG welding are employed for detailed and high-quality fabrication.
Applications of Specialized Fabrication Welding
Specialized fabrication welding is indispensable in various industries, including:
- Energy Sector: Fabrication of pipelines, pressure vessels, and heat exchangers
- Transportation: Manufacturing of train components, shipbuilding, and aircraft structures
- Heavy Equipment: Custom parts for industrial machinery and vehicles
Partnering with the Right Welding Service Provider
Choosing the right provider for industrial welding services is crucial for achieving optimal results. Factors to consider include:
- Expertise: Look for providers with a proven track record in custom and specialized welding.
- Technology: Ensure they utilize state-of-the-art equipment and techniques.
- Certifications: Verify compliance with industry standards and certifications.
- Customer Service: A reliable provider prioritizes communication, collaboration, and on-time delivery.
Future Trends in Custom Welding Solutions
The field of welding is continually evolving, driven by advancements in technology and changing industry demands. Some emerging trends include:
- 3D Printing and Additive Manufacturing: Combining welding with additive processes to create complex structures.
- Eco-Friendly Practices: Developing sustainable welding methods to minimize environmental impact.
- Augmented Reality (AR): Using AR for training and enhancing precision in welding tasks.
These innovations are set to further enhance the capabilities and applications of custom welding solutions, making them even more indispensable in the industrial landscape.
Conclusion
Custom welding solutions, bolstered by specialized fabrication welding, are revolutionizing the industrial sector. They provide unparalleled precision, durability, and versatility, catering to the unique needs of diverse industries. By embracing advanced technologies and adhering to stringent standards, custom welding ensures superior results that stand the test of time.
As industries continue to evolve, the demand for tailored industrial welding services will only grow. Partnering with experienced professionals who understand the nuances of custom and specialized welding is key to unlocking the full potential of these transformative solutions.
Need a Machine Shop in Atmore, AL?
Escofab Inc. has been dedicated to providing quality machining and fabrication since 1981! Here at Escofab Inc. we utilize fabricating and machining to your specifications. We work to fit your needs and ensure customer satisfaction. Our friendly and informative staff are eager to assist you! Give us a call or come on in today; walk-ins welcome!