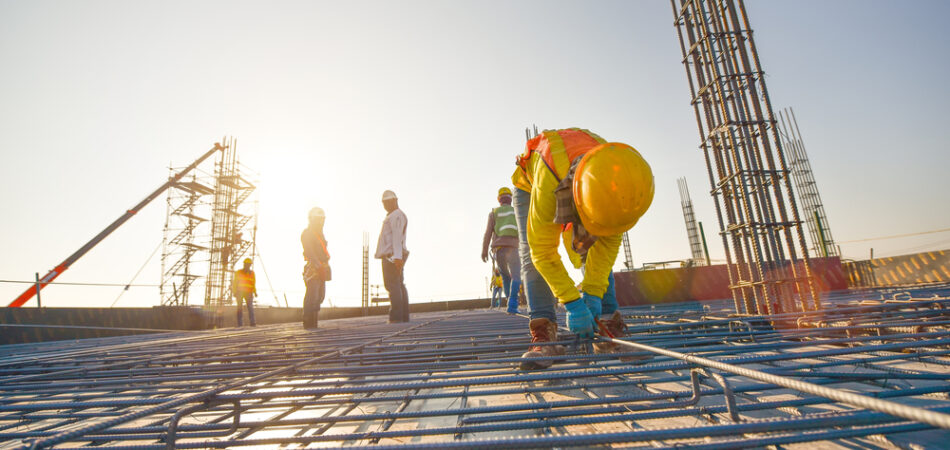
Metal fabrication is a critical industry that supports a vast array of sectors, from construction to automotive. However, this process can have significant environmental impacts, including high energy consumption, waste production, and emissions. As the world increasingly prioritizes sustainability, it’s essential for metal fabrication companies to adopt best practices for reducing their environmental footprint. This blog will explore the environmental impact of metal fabrication and outline best practices for sustainable operations.
The Environmental Impact of Metal Fabrication
Metal fabrication involves the cutting, shaping, and assembly of metal parts to create various products. While essential to modern industry, this process can have several environmental impacts:
Energy Consumption
Metal fabrication requires significant amounts of energy, particularly in processes like melting, casting, and machining. High energy consumption contributes to increased greenhouse gas emissions, especially if the energy comes from non-renewable sources.
Waste Production
The fabrication process generates various types of waste, including metal scraps, by-products, and defective parts. Managing and disposing of this waste properly is crucial to minimize environmental impact.
Emissions
Emissions from metal fabrication can include volatile organic compounds (VOCs), particulate matter, and other pollutants. These emissions can contribute to air pollution and health problems for workers and nearby communities.
Resource Depletion
The extraction and processing of raw materials for metal fabrication can deplete natural resources and lead to environmental degradation. Efficient use of resources and recycling are key to mitigating these effects.
Best Practices for Sustainable Metal Fabrication
Adopting sustainable practices in metal fabrication can significantly reduce the environmental impact of the industry. Here are some best practices for achieving more sustainable operations:
1. Energy Efficiency
Implement Energy-Efficient Technologies
Investing in energy-efficient machinery and equipment can reduce energy consumption. Technologies such as high-efficiency motors, advanced control systems, and energy-saving lighting can make a substantial difference.
Optimize Production Processes
Streamlining production processes to minimize energy use can also contribute to sustainability. For instance, optimizing cutting and machining operations to reduce energy waste can lower overall consumption.
2. Waste Management and Recycling
Reduce Material Waste
Implementing strategies to minimize material waste during fabrication is essential. Techniques such as precise cutting and advanced planning can help reduce the amount of scrap generated.
Recycle and Reuse Materials
Recycling metal scraps and reusing materials wherever possible can significantly reduce the amount of waste sent to landfills. Establishing a robust recycling program within the facility is a key step towards sustainability.
3. Emission Control
Invest in Pollution Control Technologies
Adopting pollution control technologies, such as scrubbers and filters, can help reduce emissions of VOCs and particulate matter. Regular maintenance and upgrades of these systems are crucial to ensure they operate effectively.
Monitor and Improve Air Quality
Regular monitoring of air quality within and around the facility can help identify sources of pollution and track improvements. Implementing measures to improve air quality can benefit both the environment and worker health.
4. Resource Efficiency
Optimize Raw Material Use
Efficient use of raw materials can reduce the environmental impact of metal fabrication. Techniques such as precision cutting and accurate material planning can help minimize the need for additional resources.
Support Sustainable Sourcing
Choosing suppliers that adhere to sustainable practices and source materials responsibly can contribute to a more sustainable supply chain. Supporting suppliers with environmental certifications can also align with your sustainability goals.
5. Training and Awareness
Educate Employees
Training employees on best practices for sustainability and environmental stewardship can help ensure that everyone is aware of their role in reducing the environmental impact of metal fabrication. Regular workshops and updates can keep sustainability at the forefront of operations.
Promote a Culture of Sustainability
Creating a culture that values sustainability and encourages employees to contribute ideas for improvement can drive continuous progress. Recognizing and rewarding efforts to enhance environmental performance can reinforce this culture.
Atmore AL Environmental Practices
In Atmore, AL, local environmental practices and regulations play a crucial role in shaping the approach to sustainable metal fabrication. Businesses in this area can benefit from adhering to specific guidelines and collaborating with local organizations to enhance their sustainability efforts.
Compliance with Local Regulations
Businesses in Atmore, AL should ensure they comply with local environmental regulations and standards. This includes adhering to waste disposal guidelines, emission limits, and energy efficiency requirements set by local authorities.
Collaboration with Local Organizations
Partnering with local environmental organizations and participating in community initiatives can provide valuable resources and support for sustainable practices. Engaging with local groups can also enhance a company’s reputation and demonstrate commitment to environmental stewardship.
Leveraging Local Resources
Utilizing local resources and supporting regional sustainability initiatives can contribute to a more sustainable operation. Local recycling programs, energy efficiency programs, and environmental services can provide additional support for sustainable metal fabrication practices.
Conclusion
The environmental impact of metal fabrication is significant, but by adopting best practices for sustainable operations, businesses can reduce their footprint and contribute to a healthier planet. Emphasizing energy efficiency, waste management, emission control, resource efficiency, and employee training are key steps in achieving sustainability in metal fabrication. In Atmore, AL, adhering to local environmental practices and collaborating with local organizations can further enhance these efforts. By committing to these practices, metal fabrication companies can not only improve their environmental performance but also set a positive example for the industry.
Need a Machine Shop in Atmore, AL?
Escofab Inc. has been dedicated to providing quality machining and fabrication since 1981! Here at Escofab Inc. we utilize fabricating and machining to your specifications. We work to fit your needs and ensure customer satisfaction. Our friendly and informative staff are eager to assist you! Give us a call or come on in today; walk-ins welcome!