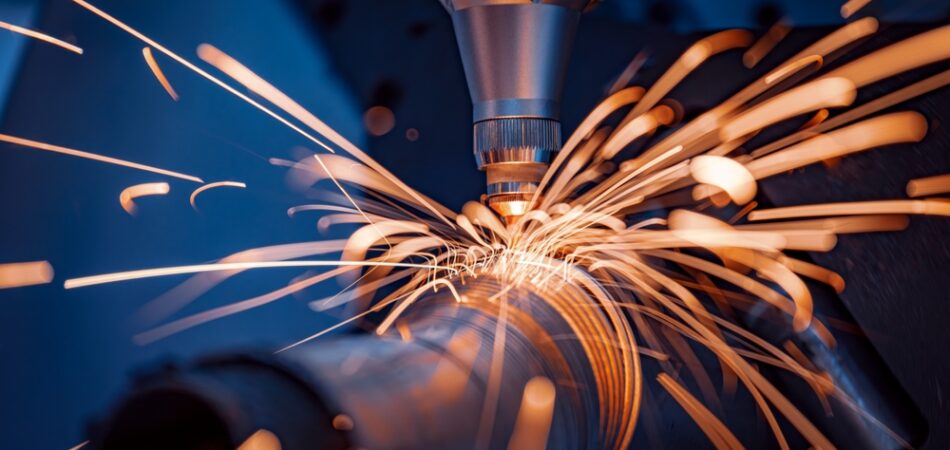
Custom metal fabrication is an essential process in modern industrial projects, allowing for the creation of specialized metal components tailored to specific requirements. This process involves cutting, bending, welding, and assembling metal structures that align precisely with engineering and architectural designs. Unlike mass-produced metal components, custom metal fabrication ensures that every piece is designed to fit the unique needs of a project, whether it be for machinery, infrastructure, or construction applications. The ability to produce metal parts with exact specifications is crucial for industries that demand precision and durability.
Industrial welding is a fundamental aspect of custom metal fabrication, allowing metal components to be securely joined to form strong structures. Welding techniques vary depending on the type of metal and the desired outcome, ensuring that each project meets the highest standards of structural integrity. This adaptability in metal fabrication makes it indispensable for industries such as aerospace, automotive, energy, and manufacturing, where even the smallest deviations in metal components can lead to operational failures. By leveraging advanced metalworking techniques, industries can enhance efficiency, improve safety, and reduce long-term maintenance costs.
The Advantages of Custom Metal Fabrication in Industrial Applications
One of the key advantages of custom metal fabrication is its ability to provide solutions that are tailored to the specific needs of an industrial project. Off-the-shelf metal components often fail to meet the unique requirements of specialized applications, leading to inefficiencies and potential structural weaknesses. Custom fabrication eliminates these issues by producing parts that fit precisely within the design parameters of a project. This ensures that industrial equipment and structures perform optimally and last longer, reducing the need for costly repairs and replacements.
Another significant benefit of custom metal fabrication is the use of high-quality materials selected to meet the specific demands of an application. From stainless steel and aluminum to carbon steel and copper, different metals offer varying levels of strength, resistance, and conductivity. Custom fabrication allows for the selection of materials that best suit the environmental conditions and operational stresses of a project. Additionally, with advanced techniques such as CNC machining and laser cutting, fabricators can achieve exceptional precision, reducing material waste and enhancing overall efficiency.
Industrial welding plays a crucial role in ensuring the durability and reliability of fabricated metal components. Skilled welders use various techniques such as MIG, TIG, and arc welding to create strong, long-lasting bonds between metal parts. This is especially important in industries that require heavy-duty machinery and infrastructure, where weak welds can lead to catastrophic failures. The expertise of professional welders in custom metal fabrication ensures that each welded joint meets the highest industry standards, providing enhanced structural integrity and safety.
The Role of Advanced Technology in Custom Metal Fabrication
Technological advancements have revolutionized the field of custom metal fabrication, making it more efficient, precise, and cost-effective. Computer-aided design (CAD) software allows engineers to create highly detailed blueprints, ensuring that every component is fabricated with exact specifications. These digital models enable fabricators to visualize the final product, identify potential issues before production begins, and optimize material usage to reduce waste. By integrating CAD with automated manufacturing processes, companies can significantly improve productivity while maintaining superior quality standards.
Another breakthrough in custom metal fabrication is the use of CNC (Computer Numerical Control) machining. This technology enables fabricators to automate cutting, drilling, and shaping processes, resulting in highly accurate and consistent metal parts. CNC machines can work with various types of metals and perform complex operations that would be challenging with manual methods. The automation of fabrication processes not only enhances precision but also reduces production time, making it an invaluable tool for industrial projects that require large-scale manufacturing.
Industrial welding has also benefited from technological advancements, with the development of robotic welding systems that improve efficiency and consistency. These automated welding solutions reduce human error and increase the speed of production, making them ideal for high-volume industrial applications. Additionally, advancements in welding materials and techniques have led to stronger and more resilient metal structures, ensuring that industrial projects maintain their structural integrity under extreme conditions. By incorporating the latest technology into custom metal fabrication, industries can enhance their capabilities and meet the growing demands of modern engineering.
The Impact of Custom Metal Fabrication on Industrial Sustainability
Sustainability has become a significant consideration in industrial projects, and custom metal fabrication plays a vital role in promoting environmentally friendly practices. One of the primary ways custom fabrication contributes to sustainability is through material efficiency. By precisely cutting and shaping metal components, fabricators can minimize waste and maximize the use of raw materials. This reduces the environmental impact associated with excess metal production and disposal, leading to more sustainable manufacturing processes.
Recycling and repurposing metal materials are also key aspects of sustainable custom metal fabrication. Many industrial projects utilize recycled metals, which not only reduces the demand for newly mined resources but also lowers energy consumption. Additionally, custom fabrication techniques allow for the reuse of metal components in different applications, extending the lifespan of materials and reducing industrial waste. By adopting sustainable fabrication practices, industries can minimize their carbon footprint while maintaining high levels of efficiency and performance.
Industrial welding also contributes to sustainability by ensuring the longevity of metal structures. Well-executed welds create durable joints that withstand environmental stresses, reducing the need for frequent replacements. This leads to lower material consumption and decreased industrial waste over time. Furthermore, advancements in welding technologies have led to more energy-efficient processes, further reducing the environmental impact of industrial metalworking. By prioritizing sustainable fabrication and welding methods, industries can achieve long-term cost savings while supporting global efforts to reduce environmental degradation.
Choosing the Right Custom Metal Fabrication Partner
Selecting the right custom metal fabrication partner is crucial for the success of any industrial project. A reputable fabrication company should have extensive experience, advanced technological capabilities, and a skilled workforce capable of delivering high-quality results. It is essential to evaluate the company’s expertise in working with various metals and their proficiency in industrial welding techniques. A reliable fabricator should be able to handle complex projects with precision and efficiency, ensuring that all components meet the required specifications.
Another important factor to consider is the company’s commitment to quality control and industry standards. Custom metal fabrication involves rigorous testing and inspection processes to ensure that metal components meet safety and performance requirements. A reputable fabrication partner should adhere to strict quality assurance protocols, using advanced testing methods to verify the integrity of fabricated parts. This includes non-destructive testing (NDT), stress analysis, and weld inspections to identify any potential weaknesses before final installation.
Customer support and project management capabilities also play a vital role in the success of a fabrication project. A professional fabrication company should offer comprehensive services, from initial design consultation to final installation. Effective communication and collaboration between engineers, fabricators, and project managers ensure that every aspect of the fabrication process aligns with the client’s expectations. By choosing a reliable custom metal fabrication partner, industries can achieve superior results, enhance operational efficiency, and maintain the highest standards of safety and durability.
Conclusion
Custom metal fabrication is a fundamental aspect of industrial projects, offering tailored solutions that improve performance, efficiency, and sustainability. With the integration of advanced technologies and high-quality materials, fabrication companies can meet the evolving demands of modern industries. Industrial welding plays a critical role in ensuring the structural integrity of metal components, further enhancing the reliability of fabricated structures. By investing in professional custom metal fabrication services, industries can achieve long-term success and drive innovation in their respective fields.
Need a Machine Shop in Atmore, AL?
Escofab Inc. has been dedicated to providing quality machining and fabrication since 1981! Here at Escofab Inc. we utilize fabricating and machining to your specifications. We work to fit your needs and ensure customer satisfaction. Our friendly and informative staff are eager to assist you! Give us a call or come on in today; walk-ins welcome!