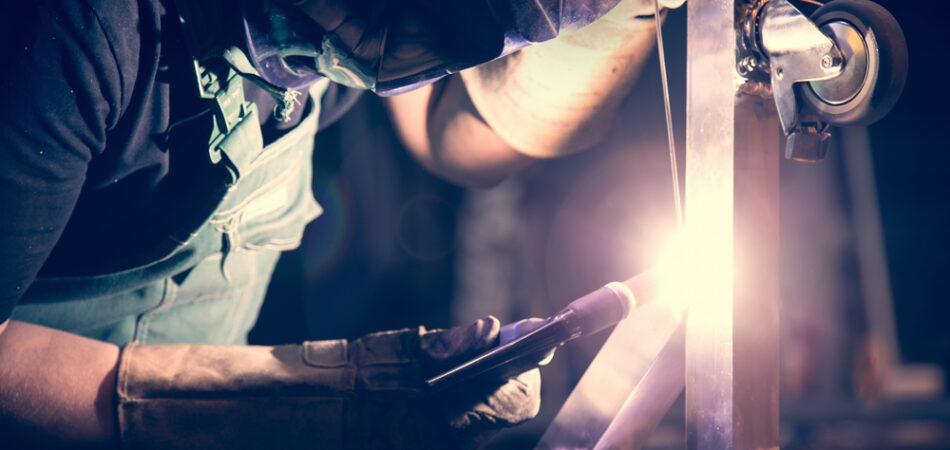
Aluminum is one of the most versatile and widely used metals in industries like automotive, aerospace, construction, and more. Its lightweight nature, resistance to corrosion, and excellent thermal and electrical conductivity make it a valuable material. However, aluminum welding presents unique challenges due to its properties, such as its high thermal conductivity and the presence of a surface oxide layer. To tackle these challenges, different types of aluminum welding techniques have been developed, each suited to specific applications. Whether you’re welding aluminum in Atmore, AL, or anywhere else, understanding these techniques is essential for high-quality results.
In this blog, we’ll explore the various aluminum welding methods, their advantages, and the scenarios where they are most effective.
Why Aluminum Welding is Challenging
Before diving into the different types of aluminum welding techniques, it’s important to understand why welding aluminum is particularly challenging compared to other metals like steel. One of the primary reasons is that aluminum has a lower melting point and higher thermal conductivity. This means the heat from welding can disperse quickly, making it harder to maintain a stable weld pool. Additionally, aluminum naturally forms a thin layer of aluminum oxide on its surface, which has a much higher melting point than the aluminum beneath it. To ensure a strong bond, this oxide layer must be properly managed or removed during the welding process.
Another issue is aluminum’s tendency to warp or crack under the stress of welding due to its thermal expansion characteristics. Selecting the right welding technique can help address these challenges, ensuring strong and durable aluminum joints.
Common Aluminum Welding Techniques
There are several aluminum welding techniques used by professionals in Atmore, AL, and beyond. Each method has its pros and cons depending on the specific application. Let’s explore these techniques in detail.
1. Tungsten Inert Gas (TIG) Welding
Tungsten Inert Gas (TIG) welding, also known as Gas Tungsten Arc Welding (GTAW), is one of the most popular methods for welding aluminum. TIG welding uses a non-consumable tungsten electrode to produce the weld, while an inert gas (usually argon or helium) shields the weld area from atmospheric contamination.
How TIG Welding Works
In TIG welding, the welder controls the heat input using a foot pedal, allowing for precise temperature control, which is crucial for aluminum. The welder manually feeds a filler rod into the weld pool to join the metals. The shielding gas protects the weld area from oxidation, keeping the weld clean and strong.
Advantages of TIG Welding
- Precision: TIG welding offers precise control, making it ideal for thin aluminum sheets or complex joints.
- High-Quality Welds: The process creates clean and strong welds with minimal spatter or imperfections.
- Versatility: TIG welding can be used on various aluminum alloys and thicknesses.
Disadvantages of TIG Welding
- Speed: TIG welding can be slow compared to other methods, making it less suitable for high-volume production.
- Skill Requirement: This technique requires a high level of skill and experience.
TIG welding is commonly used in industries such as aerospace, automotive, and manufacturing, where high-quality aluminum welds are essential.
2. Metal Inert Gas (MIG) Welding
Metal Inert Gas (MIG) welding, or Gas Metal Arc Welding (GMAW), is another popular aluminum welding technique. It uses a consumable wire electrode that is fed through a welding gun, while an inert shielding gas protects the weld from contamination.
How MIG Welding Works
In MIG welding, the electrode wire is continuously fed through the welding gun, which melts and fuses the aluminum pieces. The shielding gas, typically argon or a mixture of argon and helium, prevents oxidation during the welding process. MIG welding can be done in a fully automated setup, which makes it more efficient for industrial applications.
Advantages of MIG Welding
- Speed: MIG welding is faster than TIG welding, making it more suitable for high-production environments.
- Ease of Use: MIG welding is relatively easier to learn compared to TIG, making it accessible to welders with less experience.
- Versatility: MIG welding can be used for both thin and thick aluminum materials.
Disadvantages of MIG Welding
- Less Precision: MIG welding is less precise than TIG welding, which can result in more spatter and the need for post-weld cleaning.
- Limited Control: The constant wire feed can make it challenging to maintain control over the heat input, increasing the risk of warping or burn-through on thin materials.
MIG welding is commonly used in industries like construction and automotive, where speed and efficiency are crucial.
3. Plasma Arc Welding (PAW)
Plasma Arc Welding (PAW) is similar to TIG welding but uses a much smaller, more focused arc. In PAW, the arc is created between an electrode and the aluminum workpiece, and the plasma is forced through a fine nozzle to concentrate the heat in a small area.
How Plasma Arc Welding Works
PAW uses a high-velocity plasma stream to melt the aluminum, while an inert gas shields the weld from oxidation. The process offers excellent control over heat input, making it ideal for precision welding applications.
Advantages of PAW
- High Precision: PAW provides extremely focused heat, which is beneficial for intricate welding tasks and thin aluminum sheets.
- Deep Penetration: It can achieve deep weld penetration with minimal heat-affected zones.
Disadvantages of PAW
- Complexity: PAW requires specialized equipment and high levels of skill.
- Cost: The equipment for PAW can be more expensive than traditional TIG or MIG setups.
PAW is often used in high-tech industries like aerospace and medical device manufacturing, where precision and reliability are paramount.
4. Friction Stir Welding (FSW)
Friction Stir Welding (FSW) is a solid-state welding process that doesn’t involve melting the aluminum. Instead, a rotating tool is pressed into the joint area, and the friction generated by the tool softens the aluminum, which then mixes and bonds the materials together.
How Friction Stir Welding Works
FSW involves a cylindrical tool that rotates and moves along the seam of two aluminum pieces. The heat generated by friction softens the material, allowing it to flow and mix together, forming a strong weld without melting the metal.
Advantages of FSW
- High Strength: FSW produces strong, high-quality welds with minimal defects.
- Minimal Warping: Since the aluminum doesn’t melt, there’s less thermal distortion compared to traditional welding techniques.
- Environmentally Friendly: FSW doesn’t require filler materials or shielding gases, reducing waste and environmental impact.
Disadvantages of FSW
- Limited Applications: FSW is primarily used for long, straight welds and is not suitable for complex shapes or intricate joints.
- Specialized Equipment: The process requires specialized machinery, which can be costly.
FSW is commonly used in industries like shipbuilding, automotive, and aerospace, where long, continuous aluminum welds are needed.
5. Laser Beam Welding (LBW)
Laser Beam Welding (LBW) is a high-energy welding technique that uses a focused laser beam to melt and fuse aluminum pieces together. This method is known for its precision and is often used in high-tech applications.
How Laser Beam Welding Works
LBW uses a concentrated laser beam to heat and melt the aluminum, forming a weld. The high-energy beam allows for deep penetration and fast welding speeds, making it efficient for certain aluminum applications.
Advantages of LBW
- Precision: LBW offers excellent control, making it ideal for small or intricate welds.
- Speed: The process is fast, allowing for high production rates.
- Minimal Heat-Affected Zones: The focused laser minimizes the amount of heat applied, reducing warping and distortion.
Disadvantages of LBW
- Cost: LBW equipment is expensive, making it less accessible for smaller operations.
- Limited Thickness: LBW is best suited for thin materials and may not be as effective for thicker aluminum sections.
LBW is often used in industries like electronics, medical devices, and aerospace for applications that require precision and speed.
Choosing the Right Aluminum Welding Technique in Atmore, AL
When choosing the best aluminum welding technique, it’s essential to consider the specific application, material thickness, and desired weld quality. In Atmore, AL, industries that rely on aluminum welding range from automotive repair shops to large-scale manufacturing plants. Whether you’re a professional welder or a hobbyist, understanding these different types of aluminum welding techniques will help you make informed decisions for your projects.
By selecting the right method, you can ensure a strong, durable, and visually appealing weld, whether you’re working with thin aluminum sheets or thick structural components.
In short, the key to successful aluminum welding lies in selecting the appropriate technique based on your specific needs. Whether you’re working with TIG, MIG, or more advanced methods like FSW or LBW, mastering the right aluminum welding techniques can enhance the quality and efficiency of your work in Atmore, AL, and beyond.
Need a Machine Shop in Atmore, AL?
Escofab Inc. has been dedicated to providing quality machining and fabrication since 1981! Here at Escofab Inc. we utilize fabricating and machining to your specifications. We work to fit your needs and ensure customer satisfaction. Our friendly and informative staff are eager to assist you! Give us a call or come on in today; walk-ins welcome!