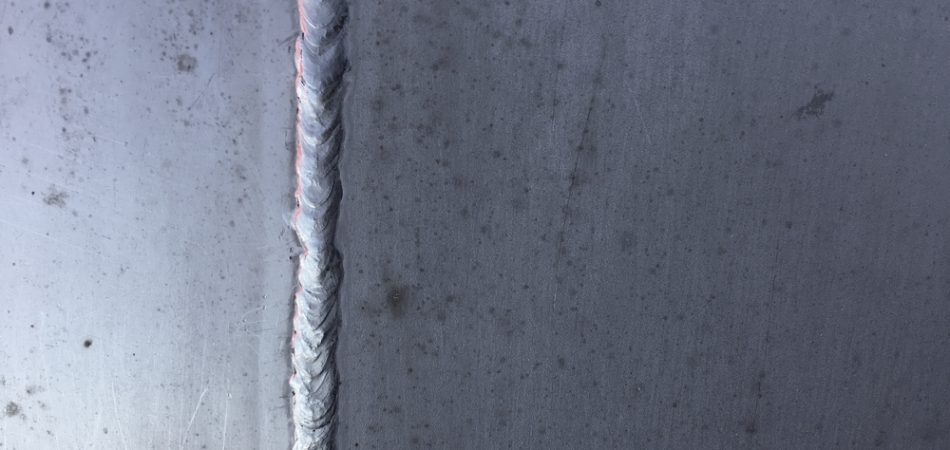
Seam welding is a popular process in the manufacturing industry, often used to join two pieces of metal together along a seam. This process involves the use of heat and pressure to create a continuous seam weld along the edges of the two pieces of metal. Seam welding is commonly used in various industries, including automotive, aerospace, and construction, due to its efficiency and effectiveness.
Seam welding can be done using various methods, including resistance welding, laser welding, and friction welding. Each method has its own advantages and limitations, but they all serve the same purpose of joining two pieces of metal together. One of the main advantages of seam welding is its ability to create a strong and durable bond between the two pieces of metal, ensuring that they stay together even under extreme conditions.
For beginners who are new to the world of manufacturing and welding, seam welding may seem like a complex process. However, with the right guidance and understanding, anyone can master the art of seam welding. This guide will provide you with all the information you need to understand seam welding and its applications in the manufacturing industry.
Understanding Seam Welding
Seam welding is a process that involves the use of heat and pressure to create a continuous weld along the edges of two pieces of metal. This process is often used to join thin metal sheets together, creating a strong and durable bond. Seam welding can be done using various methods, including resistance welding, laser welding, and friction welding.
In resistance welding, an electric current is passed through the two pieces of metal, creating heat that melts the edges of the metal sheets. Pressure is then applied to the two pieces of metal, creating a seamless weld along the edges. Resistance welding is a fast and efficient method of seam welding, making it ideal for high-volume manufacturing processes.
Laser welding, on the other hand, uses a high-powered laser beam to melt the edges of the metal sheets and create a weld. Laser welding is a precise and accurate method of seam welding, making it ideal for welding complex and intricate designs. However, laser welding can be more expensive than resistance welding, making it less suitable for high-volume manufacturing processes.
Friction welding is another method of seam welding that involves rubbing the two pieces of metal together to create heat and friction. This heat and pressure are used to melt the edges of the metal sheets and create a weld. Friction welding is a versatile method of seam welding, as it can be used to weld a wide range of materials, including aluminum, steel, and titanium.
Applications of Seam Welding
Seam welding has a wide range of applications in the manufacturing industry, including automotive, aerospace, and construction. In the automotive industry, seam welding is commonly used to join the body panels of cars together, creating a seamless and aerodynamic design. Seam welding is also used in the aerospace industry to create fuel tanks, fuselages, and other structural components.
In the construction industry, seam welding is often used to join metal sheets together to create roofs, walls, and other structural elements. Seam welding is a cost-effective and efficient method of joining metal sheets together, making it ideal for large-scale construction projects.
What to Know About Seam Welding
When it comes to seam welding, there are a few key points to keep in mind. First, it is important to use the right method of seam welding for your specific application. Each method of seam welding has its own advantages and limitations, so it is important to choose the method that best suits your needs.
Second, it is important to have the right equipment and tools for seam welding. This includes welding machines, electrodes, and protective gear. Using the right equipment will ensure that your seam welding process is safe and efficient.
Finally, it is important to practice proper safety precautions when seam welding. This includes wearing protective gear, such as gloves and goggles, and following all safety guidelines and procedures. By following these tips, you can ensure that your seam welding process is successful and effective.
Summary
Seam welding is a versatile and efficient process that is widely used in the manufacturing industry. By understanding the basics of seam welding and its applications, you can master the art of seam welding and create strong and durable bonds between two pieces of metal. Whether you are a beginner or an experienced welder, seam welding is a valuable skill to have in your repertoire.
Need a Machine Shop in Atmore, AL?
Escofab Inc. has been dedicated to providing quality machining and fabrication since 1981! Here at Escofab Inc. we utilize fabricating and machining to your specifications. We work to fit your needs and ensure customer satisfaction. Our friendly and informative staff are eager to assist you! Give us a call or come on in today; walk-ins welcome!