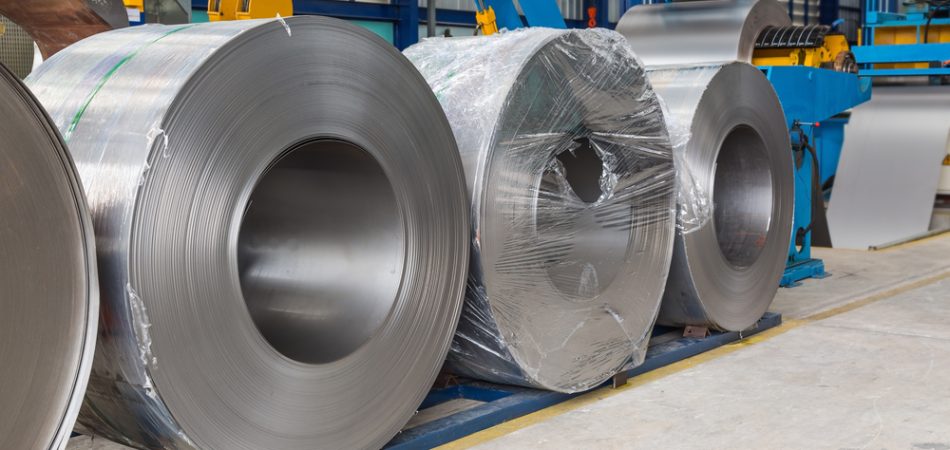
Sheet metal fabrication is a crucial aspect of many industries, from automotive to aerospace. This process involves cutting, bending, and assembling metal sheets to create a wide range of products, from small components to large structures. Mastering sheet metal fabrication requires a combination of skill, knowledge, and the right tools. In this step-by-step guide, we will walk you through the process of sheet metal fabrication, highlighting key techniques and considerations.
Understanding the Basics of Sheet Metal Fabrication
Before delving into the specifics of sheet metal fabrication, it is essential to have a basic understanding of the materials and tools involved. Sheet metal is a versatile material that comes in a variety of thicknesses and types, such as aluminum, steel, and copper. The choice of material will depend on the application and the desired properties of the final product.
In terms of tools, a typical sheet metal fabrication workshop will include equipment such as shears, brakes, and presses. Shears are used for cutting metal sheets to size, while brakes are used for bending and shaping the metal. Presses are utilized for punching holes and forming intricate shapes.
Step 1: Design and Planning
The first step in the sheet metal fabrication process is designing and planning the project. This involves creating a detailed blueprint or drawing that specifies the dimensions, shape, and tolerances of the final product. The design phase also includes determining the type of material to be used and selecting the appropriate tools and techniques for fabrication.
Step 2: Cutting
Once the design is finalized, the next step is cutting the metal sheet to the required size. This can be done using shears, a plasma cutter, or a laser cutting machine, depending on the complexity of the design and the precision required. Careful measurements and precise cutting are essential to ensure the pieces fit together correctly during assembly.
Step 3: Bending and Shaping
After the metal sheet is cut to size, the next step is bending and shaping it to achieve the desired form. This is typically done using a brake press, which applies pressure to the metal sheet to bend it at a specific angle. The bending process requires precision and control to ensure the final product meets the design specifications.
Step 4: Forming and Assembly
Once the individual components are cut, bent, and shaped, they are ready to be assembled into the final product. This involves welding or fastening the pieces together using techniques such as spot welding, TIG welding, or riveting. Care must be taken to ensure the components are aligned correctly and securely attached to each other.
Step 5: Finishing Touches
After the components are assembled, the final step is to add any finishing touches, such as grinding sharp edges, deburring rough surfaces, or applying a protective coating. These finishing touches not only enhance the appearance of the product but also improve its durability and functionality.
Summary:
Mastering sheet metal fabrication requires a combination of skill, knowledge, and the right tools. By following the step-by-step guide outlined above, you can gain a better understanding of the sheet metal fabrication process and improve your proficiency in this essential manufacturing technique. Whether you are a beginner or an experienced fabricator, these techniques and considerations will help you achieve quality results in your sheet metal fabrication projects.
Need a Machine Shop in Atmore, AL?
Escofab Inc. has been dedicated to providing quality machining and fabrication since 1981! Here at Escofab Inc. we utilize fabricating and machining to your specifications. We work to fit your needs and ensure customer satisfaction. Our friendly and informative staff are eager to assist you! Give us a call or come on in today; walk-ins welcome!